In this experiment you will make an electromagnet. Then you will test how changing two variables can affect its strength. Safety: Electromagnets can get hot
It is the magnetic force obtained in the solenoid after finishing the stroke using standard power . Remanent Force: It is the force remaining after switching
8 déc. 2021 should be de-attachable from both the Power supply and the electromagnet side to facilitate easy transportation.
Describe how the students could build an electromagnet. Include in your answer how the students should vary and test the strength of their electromagnet.
Electromagnet Designs on Low-Inductance Power. Flow Platforms for the Magnetized Liner Inertial. Fusion (MagLIF) Concept at Sandia's Z Facility.
Magnets and Electromagnets. Can you make a magnet from a nail some batteries and some wire? Problems. Research. Can the strength of an electromagnet be
As current in the electromagnet varies so does the force on the compass needle. Electricity flowing through a wire creates a magnetic field around that wire.
A student is investigating the strength of electromagnets. Figure 1 shows three electromagnets. The student hung a line of paper clips from each electromagnet.
14 juil. 2016 The approach of this research paper is to find out the effect of the temperature on the strength of electricity.
POWER SUPPLY OPTIONS: • Front panel mounted indicator lights. • AC pilot light (Input voltage “ON”). • DC pilot light (Indicates magnet power "ON").
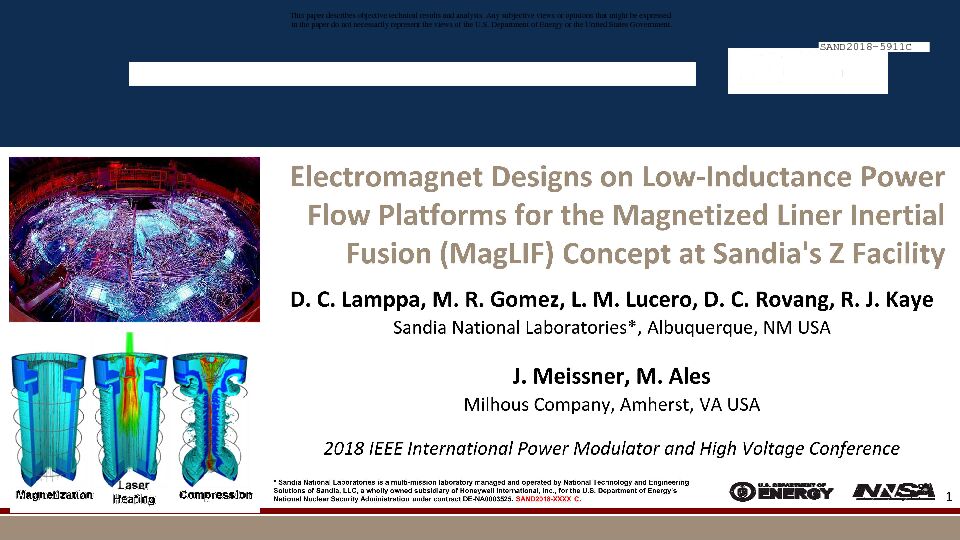
860_31524964
Magnetization Hea ingCompr s ion
Electromagnet Designs on Low-Inductance Power
Flow Platforms for the Magnetized Liner Inertial
Fusion (MagLIF) Concept at Sandia's Z Facility
D. C. Lamppa, M. R. Gomez, L. M. Lucero, D. C. Rovang, R. J. Kaye Sandia National Laboratories*, Albuquerque, NM USA
J. Meissner, M. Ales
Milhous Company, Amherst, VA USA
2018 IEEE International Power Modulator and High Voltage Conference
" Sandia National Laboratories is a multi-mission laboratory managed and operated by National Technology and Engineering
Solutions of Sandia, LLC, a wholly owned subsidiary of Honeywell International, lnc., for the U.S. Department of Energy's
National Nuclear Security Administration under contract DE-NA0003525. SAND2018-XXXX C.IISMCW.1SAND2018-5911C
This paper describes objective technical results and analysis. Any subjective views or opinions that might be expressed
in the paper do not necessarily represent the views of the U.S. Department of Energy or the United States Government.
Outline of today's discussion
n Sandia's Z Machine and the MagLIF concept n Pre-magnetizing the fusion fuel with the Applied B on Z (ABZ) system n Making a more efficient inefficient coil: Designing an electromagnet for Low-L n The path forward to 20 - 25 T
El Page...t.
SANDIA'S Z MACHINE AND THE MAGLIF CONCEPT
Sandia's Z Machine uses large currents (>25MA) to generate 100-MBar pressures for HEDP experiments II r -0441 1 10 4 -NI 6,
751111 ari a t
'.1 33 m
diameter 80
605
1(5 40
ci 20
Marx generators
pulse-forming lines insulator stack 67 TW 20TW
0.51 1.5
time (vs) 2.5
SandiaNationalLaboratories
Magnetically-Driven Implosion
MBar drive current Implosion time - 50 ns; stagnation - 0.1-1 ns100 MBar at 26 MA and 1 mm Magnetized Liner Inertial Fusion (MagLIF) combines three stages that reduce fuel compression requirements to achieve fusion conditionsApplied + B-field A Laser entrance hole Liner
Cold DT fuel
Axial B-field
Pre-Magnetization
Compressed
B-field
Current A
AAA
Current-
generated
B-field
''.......-...." &
Z-Driven lmplosion
Liner unstable but
sufficiently intact
Compressed fuel reaches
fusion temperatures r
AppliedLaser heated B-field
fuel
Liner beginning
compression
Azimuthal
drive field
Laser Pre-Heat
SandiaNationalLaboratories
Laser 20(a)
B-field
L /j.....,--- ->.
29503000 3050Time [ns]3100
S.A. Slutz et al., Phys Plasmas (2010); A.B. Sefkow et al., Phys Plasmas (2014); M. R. Gomez et al., Phys. Rev. Lett. (2014). 5
Pre-Magnetization relaxes implosion convergence
requirements by helping confine heated fuel
Without Magnetic Field
With Magnetic Field
Time-integrated x-ray
self-emission seen in radiographs Low B L._ A 1-Z
High B
When magnetized, MagLIF Liners have reduced x-ray
self emission (left) and particles are confined within fuel on cyclotron orbits (right)
Neutronsil
.e12 100
SandiaNationalLaboratories
10 L 1 0 derv±0.7 den=1.1 1=1.8 den=3.0 30 20 20 30
ti i Energy Deposited (kJ) 10 Fusion yield trends for various fuel density, laser preheat energy benefit from increased magnetic flux density • A highly magnetized fuel inhibits loss by trapping electrons to axial field lines and reducing radial thermal conduction to cold liner wall • The usual azimuthal MRT instability becomes helical; initial B-field may stabilize the liner during compression to improve fusion conditions 6
PRE-MAGNETIZING THE FUSION FUEL WITH THE
APPLIED B ON Z (ABZ) SYSTEM
The Applied B on Z (ABZ) capacitor and coil system designed to provide 10 30 T within liner volume • Two 4-mF, 15-kV capacitor banks store 900kJ total. • Paralleling diodes, 125mQ overcurrent protection per bank. • Switchyard dummy load inductor available for system checks. • 0.8 - 3mH coils ensure 2-6ms risetimes for magnetic diffusion •Vacuum feedthrough utilizes encapsulated transition between coaxial cable drive and coil loads /
SandiaNationalLaboratories
Z Center Section Vacuum Chamber
Magnetic Field Coil
Assembly on Z
Center Section
• •
Cable Header
Capacitor Bank #1q
C=4 roF
R = 11.8 rnri
ABZ Bank 1
ABZ Bank 2
6.2 roCI
6X 24' DS2168
6X 28' OS2168
Capacitor Bank #2q
Switchyard Test load
124rn0
Current limiting
resistors 124m0
l 19.1 mr) 13.6 mLi0.9-2mH
8X 182X 35'R -132-1140ID5.2323 1SC3052323
Junction
Box /Switchyard and protection circuitry
Verification
coil
Vacuum
feedthrough
Junction
box
C=4 ttIF
=11.8 mr1
6.2 mC1
D. C. Rovang, et al, Rev. Sci. lnstrum. 85, 124701 (2014)8
Integrating electromagnets onto the target
geometry requires changes in Z power flow • Initial guidance was to prioritize radial diagnostic access and • field uniformity in liner
1Top Coil
X-ray diagnostics
Ir-Bottom
L Coil
Anode
L - 17MA Drive Current
r=2.5cm • We designed coil pairs with 1-2.5cm axial spacing • An Extended Power Feed was needed to raise target above the bottom coil of a split pair into uniform field region • ABZ coil pairs consist of an 80-turn top coil and either a 60- or
80-turn bottom coil
MagLIF
Liner
SandiaLIM NationalLaboratories
• Helmholtz-like pairs provide <1% field uniformity • 5cm-bore coils magnetize - 75cm3 region to 10 - 20 T
Magnetic
Field
(T) 10.12 10.1 10.08 10.06
10.040 2 4 6 8
Axial Distance (mm)
10.06 - •
7, 10.04
u: c 10.02
10 0 2 4 6
Radial Distance (mm)
2D Transient magnetic calculations axial and radial
lineouts showing -1% field variation within liner9
The Extended Power Feed platform was designed
with three coil configurations in mind
Full-Access Spacinq (60-80)
• 10-T Operating point • - 25-30mm coil spacing for radial diagnostic access • 90+ shots on Z since 2013
Limited-Access Spacinq (80-80)
15-T Operating point
- 10-14mm coil spacing for radial diagnostic access
15+ shots on Z since 2013
No-Access Spacinq (230-turn)
20-25-T Operating point
No radial diagnostic access
Never shot on Z in this
configuration ...
SandkiNationalLaboratories
10
The Extended Power Feed limits achievable drive
pressQures from the Z current pulse 10r 0 -10 E -20 o o • -300_ -40 -50 -60 -70
Bottom Coil
10 20 30 40 50 60
radial position [mm]
Sandiaa mit NationalLaboratories
• Each additional nH of initial feed inductance reduces deliverable machine current by -0.8 MA • Higher power feed voltage drives nonlinear loss mechanisms • Z's magnetic drive pressure should increase in step with ABZ field and laser preheat energy to maintain liner convergence • We are also already near the Z Facility's peak charge voltage
The extended power feed results in
initial load inductance of 7.2nH 100.0
1.0 0.1
Imax=17.4 (7.2 nH 80 kV)
Imax=21.1 (4.5 nH 90 kV)
lirrax -22.6 (3.5 nH 95 kV)
010 20 30 40 50
Bz Tesla
Fusion yield increases with magnetic field and drive current11
By reducing feed inductance, Z can deliver
more current to a Ma • LIF liner -20 -25 0 10 20 30 40 50 60 radial position [mr] E 0 o o0_
Ei -10
-15 -20 -250 10 20 30 40 50 60 radial position [mm] (C) 4.0nH -250 10 20 30 40 radial position [mm] Initial inductance is reduced by lowering axial extent of feed (A), reducing power feed A-K gap (B), and return can volume (C)
25.0
20.0 15.0
10.0 -
5.0 -
SandiaNationalLaboratories
2.5 nH
3.5 nH
4.5 nH
5.5 nH
6.5 nH
0.0 2950 3000 3050 3100
Time (ns)
Simulated load current profiles for varying final
power feed inductances and imploding MagLIF liner Hutsel, et a ., PhyRev AccelBeams, 21, 030401 (2018) 12 The " 5 . 1 n H Low-Inductance (Low-L) platform uses
230-turn coil to magnetize MagLIF linerg_
-1cm
Diagnostic
accessAnode
Current Flow
SandiaNationalLaboratories
AO622A1 Calculated IN for 7.5mm tall target - ABZ Vein, 110.5kit, !peak = 8.4 kA 14 12 • p 10 c 8 LT_ 6 czi)co24
I z=7.5mm 2
z=3.8mm z= Omm •
X: 4.7
Y: 12.99
X: 4.7
Y: 10.34
-z=ornm z=3.75mm z=7.5mm
0 0.6 11.5 2 2,6 3 3.6 4 4.5 5 5.5
Ti me (ms)
ANSYS Maxwell Transient-Magnetic calculations predict -23% axial variation of field in 7.5mm tall target (above); -32% for lOmm tall target 13
It is remarkably inefficient to utilize the
external field of the 230-turn coil like this
B [tesia]
1 26.0
24.3
22.6
20.8
19.1 17.4 15.6 13.9 12.2 10.4 8.7 7.0 5.2 3.5 1.8 0.0
Coil Envelope
Field distribution at 4.2ms (time of Z trigger)
• • . • .
SandiaNationalLaboratories
Coil was designed to produce 25-T at coil midplane for No Access configuration Not enough headroom in bank voltage for Bz_ayg > 12-T By reducing coil height by 50% (230 4 115 turns), average Bz at target drops by only 6%! Adding 2 outer radial layers would increase field by 18%!
We can design a better coil for this application.
24.00
Coil Midplane Lineout
Curve Info
- 1131
Liner Top
(z = lOmm)
NameXY
m 137.7450.12..9014 m247.54149.2923
Liner Bottom
= Dm m) " I '10.0030.00
Distance [r-nr-n]
I '4000I '50.00 60.00
MAKING A MORE EFFICIENT INEFFICIENT COIL:
DESIGNING AN ELECTROMAGNET FOR LOW-L
Program guidelines dictate ABZ coil design path
The MagLIF program looks to increase constituent parameters in lockstep • Integration by September 2018: • ABZ field between 15 - 20 T • Z Machine delivering 19 - 20 MA • Laser preheat of 1 - 2 kJ • Integrated by September 2020: • ABZ field between 20 - 25 T • Z Machine delivering 20 - 22 MA • Laser preheat of 2 - 4 kJ
SandkiNationalLaboratories
16
Coil Design Requirements
• Flux Density: • Low-L Coil shall be able to magnetize target to 15-T average across the liner. • Low-L Coil should be able to magnetize target to 20-T average field across the liner. • Liner Uniformity: Equal or lower than existing Low-L platform: - 32% across 1.0mm target. • This is a lower priority than flux density. • Bank Dynamics: • Rise time should be < 6.1 ms
• Low-L Coil shall achieve requirements with one-bank operation at 13.5kV max (limits coil inductance)
• Lifetime and pulsed behavior: • Low-L Coil should achieve required field strengths using - 10kA current
Enables coupling to 60- and 80-turn coils
• Demonstrate coil lifetime of n=10 shots at required field strengths
SandiaNationalLaboratories
17 Loosely constrained parameter space required staged analysis SandiaNational approach to "optimize" output design Laboratories
Parameters
• Initial coil diameter • Axial layers (how "tall" is it) • # of zylon internal reinforcement shells • Thickness of zylon reinforcement shells • Outer coil radius rMATLAB field calculations - Calculate Bz(0, z) - Calculate Rpc, Lijc - Turn geometries (r,z)
RDC, LDC
lGeometries,
Shell pressures
. .
Drive V, I
MATLAB ABZ bank modeler
- Time of peak current (Tpk) - Vchg required - Ohmic heating of coil - Emag, Ealec, and efficiency
1000s of runs
Maxwell 2D Magnetostatic Geometries
- Confirm Lijc - Verify Bz (0, z) - Bulk Lorentz forces (r,z)
Surveyed parameter space yielded
-3400 design variants
Distributed Lorentz Forces
lOs of runs t-
Maxwell 2D Time-harmonic
- Confirm Rpc
Estimate RAc
\
ANSYS Mechanical Static Structural
Utilizing nonlinear solver, nonlinear Cu alloy model, orthotropic zylon model - Stress as a function of radius - Elastic, plastic strains as a function of radius - Bulk Lorentz forces (r,z)
1 f ,,1 o vi 1 uno
3- and 4-shell variants of 13-axial-layer coil advanced to detailed design
10 -10E -20-c -30 • -40 -50 -60
1010131313131313131310101313131313131313101013131313131313131013131MIMEMIMI1013131MIMIMMI1013131MIMEMIMI1013131MIMEMIMI1013131MIMEMIMIE113131EMMIMI
AIMIMIE1131313131313•113131311111111113131313
020 40 60
Radius (mm)
80
10
WEIMIMEIMEMODZIMMIDDIMIDZIDIDZIMODZI
-10DO DODO DODIDZIMODZIDIDZIMODZIDO DODIDZIMODZIDO DODIDZIMODZI -20 c3)
DO DODO DOmM
DIDZIMODZIDIDZIMODZIDIDZIMODZIoDIDZIMODZI-30 DODIDZIMODZIxxxx XX XXX XXX -40 -50 -60
0 20 40 60
Radius (mm)
80
MATLAB-generated 3-shell and
4-shell Low-L coil geometries
n
Etesla]
• 1 28.0
26.1
24.3
22.4
20.6
18.7 16.8 15.0 13.1 11.2 9.4 7.5 5.7 3.8 1.9 0.1
I IL Dr.:4111%N wirhr.
1.11 0.9mm
ANSYS Maxwell-Generated
magnetic field strengths and
JxB distributed force loadings
[ a NiIrr3frffrh...
1)....1-1.1. 411
;:.id. 7re.! 110,..., r...
0.3mm I
_
ANSYS Mechanical-generated total deformation
using elastic-plastic nonlinear copper model for
20-T average field at liner location
Z hardware imposes unique winding requirements to enable novel internal reinforcement, coil connection scheme •.
3-shell Low-L Coil
111".1.!!!!timiniasieshwr
e"-
4-shell Low-L Coil
• Designs minimize material below coil • Inter-coil connections made via crimps above coil in lower-field regions • Requires a "down-wind" and "up- wind" to get wire out of way for zylon
SandiaNationalLaboratories
3-shell Low-L Coil
Delrin flange captures coil• Allows for internal reinforcement transitions and leads for final around clean breaks in conductor wind epoxy encapsulation process o
3-Shell and 4-Shell Low-L Coils perform similarly in simulation
Parameter3-Shell4-Shell
Coil Inductance
DC Resistance
Drive current to achieve 15-T avg.
1-Bank Voltage Vchg for Bavg = 15-T
Field Uniformity for lOmm liner
2.14mH
143mQ
9.05kA
9.9kV 30%
2.27mH
153mQ
9.3kA
10.5kV
29%
Shell 1 Zylon Peak Stress1.15 GPa1.16 GPa
Shell 2 Zylon Peak Stress
Shell 3 Zylon Peak Stress
Bavg linearly scaled to 13.5kV max Vchg
Shell 1 Zylon Peak Stress at 13.5kV Vchg
Shell 2 Zylon Peak Stress at 13.5kV Vchg
Shell 3 Zylon Peak Stress at 13.5kV Vchg
1.12 GPa
1.10 GPa
20.5 T
2.14 GPa
2.08 GPa
2.04 GPa
1.10 GPa
1.04 GPa
19.3 T
1.66 GPa
1.57 GPa
1.48 GPa
Shell 4
0.62 GPa
Shell 4
0.88 GPa
Zylon fibers measured to have 3.3 GPa ultimate tensile strength for 77.5% fill fraction [Y.K. Huang et al / Composites: Part B 33 (2002)]. We assume we have less than this fill fraction.
SandiaNationalLaboratories
Zylon shell
Zylon shell
Zylon she I
3-shell sectioned prototype shows well-
filled zylon reinforcement shells, tightly- packed winding journals
3-Shell Low-L coil seems superior to 4-shell in
theory, but ... • Passing orthotropic "thick-shell" zylon ultimate tensile strength calculations is necessary for "good" designs • But not sufficient to predict coil failure. • We've never failed a zylon shell. • 3rd coil conductors are observed to move. • Observed failures always occur at wire- to-wire interfaces • Predicting lifetime would require 3D modeling based on local wire loading • Also need to consider 3D effects on layer- to-layer transition, lead-to-wire
SandiaNationalLaboratories
• A third internal reinforcement shell: • Reduces field 5% (1T out of 20T) • Increases inductance (lower Ipk at 13.5kV) • More complex to produce per unit • But it also: • Reduces calculated peak wire strain by 67% • Reduces compliance in winding journal and resultant deformation • Is likely necessary for higher-field shots (>15-T) First 3-shell coil prototype (Delrin flange removed) after 10 shots at 17-T average B-field. r 22 Prototype 3-shell coils have demonstrated n"10 for Bavg > 15-T • 15-T Bavg 100% design stress • Test coil 1: • 1 shot each at 50%, 70%, 80%, 100%, 120% • 10 shots at 133% • (Dissected after 10th shot) • Test coil 2: • lea. at 50%, 3ea. at 67%, lea. 85%, 100% • 14 shots at 120% • Soft failure of 14th shot • Test coil 3: • lea. at 50%, 67%, 85%, 100% • 9ea. at 120% • Soft failure on 9th shot (after peak current)
SandiaNationalLaboratories
Shhoot 3t 1
- Shot 2 s
Shot 4
Shot 5
Shot 6
Shot 7
Shoth8S10oJu
2 4
Time (ms)
6810
Prototype 1 pulsed ten times at 10.4kA (Bavg - 17T) before post-mortem MMI
4590 (rnm)
Coils tested in surrogate geometry that mimics Z hardware23 Observed failures have been "soft"; result from conductor movement shorting between layers during pulse n 3-shell Low-L coil is observed to accumulate large radial displacement in outer coil n This trend is observable in coil inductance (Leg oc d) n The two nested 2-layer coils see no change throughout testing n This movement eventually shorts out turns during pulse n Typically occurs after peak current (peak mechanical strain) n Does not destroy the coil (it remains intact for post-mortem)
Shotinner CoilMiddle CoilOuter CoilFull Assembly
21.6 uH 33.9 uH 1.554 mH 1.98 mH
1100.0%100.0%100.0%100.0%
299.7%100.0%100.3%100.2%
100.4%100.3%100.6%100.4%
4100.2%100.2%100.9%100.6%
5100.1%100.0%101.1%100.7%
6100.3%100.2%101.3%100.9%
799.7%100.2%101.6%101.1%
899.4%100.1%101.7%101.2%
999.8%100.2%101.9%101.3%
10 99.5%100.2%102.0%101.4%
Sandia'Mil National---.P Laboratories
Unscaled
dl/dt (V) 0.2 0.15 0.1 0.05 0 -0.05
I Shot 1
Shot 2
Shot 3
Shot 4
Shot 5
Shot 6
Shot 7
Shot 8
Shot 9
024 6 8 10
Time (ms)
Rogowski probe (di/dt diagnostic) shows gentle short after Ipk on shot 9
Test coil is nested and total coil inductance change per shotTurn movement (left arrow) and increase in inner diameter (right arrow)4
The 3-Shell Low-L coil has been fielded for 10-T
Z experiments, ready for 15-T Bavg
Experiment Z3207 (05Feb2018) utilizing 3-Shell
coil on Low-L platform for MagLIF experiment
SandiaNationalLaboratories
• We have fielded these coils on Low-L platform Z experiments at 10-T • Experiments performed in February 2018 • 15-T average field experiments currently scheduled for July 2018 • The lifetime data with the 3-shell prototypes gives us confidence in our readiness • We can increase pre-magnetization field level in standard feed experiments • Replacing 80-turn coil with 3-Shell Low-L coil to increase from 15 to 20T 25
THE PATH FORWARD TO 20 25 T
Low-L coil provides three configurations for MagLIF scaling studies
100(mm)
Low-L Coil on Low-L Platforms
15 - 20T avg. field
with 19-20MA feed designs r- rin Inn pin
80-turn Coil + Low-L Coil
20 - 22T avg. field in Standard Feed
(-17 MA drive current) 70
60
50
40
E E 30
o o0_
To 20•R
10 0 -10 -20
SandiaNationalLaboratories
I-I00 00000003000000I
I I I 1 I O 00 00 00 00 no nn O O
000003000000
000003000000
00000:-)000000
O OO OOI
1 ' i I I I oo oo00 00 00 00 nn nn oc00003000000000003000000
000003000000
nn000-)000000 I 1 I I 1 I 1 00 00 00 00 00 00
000003000000
000003000000
000003000000
. I 1 1
I." -
1 II ir_ xxxxxx_1xxxxxxxxxix i xxxxxxxxxxxxxx- xxxxxxxxxxxxx•xxxxxxxxxxxxx•xxxxxxxxx_xxxxxxxxxx•i i_ i i _ _ __ _ _ i i•
10 20 30 40 50
radial position [mm] 6070
New conformal bottom coil to increase field,
provide better field uniformity for 20-30T goal 27
Design underway to complement Low-L coil with new
bottom coil "Cheyenne" for 20-30 T operation axial position [mm] 70
60
50
40
30
20 10 -10 -20
11 IO 0 0
I 0
I 0 0 0
. 0 0 0 i 0 0 o ,,11 O 0 0 O 0 0 O 0 0 O n n O 0 0 O 0 0 O 0 0
O 0 0 0 0 0
O 0 0 0
O 00000
O 00000
O 0 0 0 0 0
O 00000
O 00000
O 00000
n nonnn
O 00000
O 00000
O 00000
3000
3000
3 0 0 0
3 0 0 0
--) n n n O 0 0 oO 0 0 O 0 0 O 0 0 O 0 0 O 0 0 O 0 0 O n n
0 00000 0
0 00000 0
3 00000 0
hiX x xx xx xx xx xx x xx xx xx xx
X XXXX XXXX
X XXXX XXXX
X XXXX XXXX
X XXXX XXXX
X XXXX XXXX
X XXXX XXXX
or 4-shell Coil
11111111
v L -. v -+ -. v -, v -. v -, , . _ 1111
1
New conformal
bottom coil "Cheyenne"
0 10 20 30 40 50 60 70
LI Fik LaboratodesNati°1Sandkilei
$k:1 {: .4: .:, k: o40 111
1 Superposition of calculated coil fields look encouraging for "25T experiments in 2020 35
30
25
ca2 10
Axial Field Lineout for 2020 design point
J
Notional MagLIF
liner location -20 0 20 40 60 80 100
Axial Distance (mm)
I= • • • • 71 • ,111 • NM •
SandiaNationalLaboratories
X: 35.75 LY: 26.72
X: 25.£Y: 23.6
. .• • Conceptual coil pair can generate 25.2-T average field at the same operating current (10kA) as the existing Low-L coil • Need to evaluate transient coil self-forces, coil attraction, and repulsion from anode Cheyenne concept requires new winding capability, fabrication process, and detailed analysis to converge on design ........
NIMINSONNM MUNN.
040
Conceptual coil design with support flange and
notional internal reinforcement shells • Tight geometric constraints prevent coil-coil transitions like in Low-L coil • Coil cross-section must follow power flow contour • Minimize Z power feed inductance • Maximize field strength per turn • Power feed and bottom coil must be designed in tandem to achieve optimized performance for both
SandiaNationalLaboratories
Machine with orbital winding functionality currently in fabrication by collaborators at Milhous Company • Space constraints require the ability to wind zylon while maintaining conductor feed under tension • Zylon winding heads must "orbit" stationary coil mandrel while wire feed remains unbroken • Orbiting heads must be preloaded with zylon • Hoping for Cheyenne prototypes by February 2019 30
Summary of today's discussionSandiaNationalLaboratories n Sandia's MagLIF program on Z requires electromagnets to pre-magnetize the fusion fuel n The magnetic field reduces thermal conduction losses in fuel, relaxes convergence requirements
n The ABZ subsystem on Z regularly delivers 10 - 15 T to Z experiments with - 16-17 MA machine current.
The ABZ team works to meet program goals for integrated MagLIF experiments: n 19-20 MA machine current, 15 - 20T pre-magnetization, 1-2kJ laser preheat
n The Low-L platform increases machine current by dropping extended power feed, reducing load inductance
n We have designed an internally reinforced magnet that can deliver 15 - 17 T average field in MagLIF liner
n Coil prototypes have demonstrated acceptable lifetime and are ready for Z experiments n Our first 15-T experiments are scheduled for July 2018 on Z n 20-22 MA machine current, 20 30T pre-magnetization, 2-4kJ laser preheat
n Our team is designing a coil pair to meet this field requirement also while providing radial diagnostic access
n A coupled design effort for the Z power feed and bottom ABZ coil is required to optimize performance
n A new winding methodology is currently in development to enable production of Cheyenne prototypes 31
Questions?