BALANCE OF CHEMICAL AND PHYSICO - ScienceDirect com
www sciencedirect com/science/article/pii/0032395081901076/ md5=22dc23c38c173ecc54a80edd19ed222f&pid=1-s2 0-0032395081901076-main pdf
BALANCE OF CHEMICAL AND PHYSICO-CHEMICAL TRANSFORMATIONS IN SOLUTIONS OF POLYAMIC ACIDS ON STORAGE * N G BEL'VIKEVICtt, V M DE~'ISOV, L N Ko~zm~vlN
Chemical Transformations in Individual Ultrasmall Biomimetic
web stanford edu/group/Zarelab/publinks/zarepub605 pdf
into in vivo reaction conditions Various approaches exist for carrying out chemical reactions in aqueous solutions at small dimensions (3–7)
Reactions in Solutions - Springer
link springer com/content/ pdf /10 1007/978-1-4020-4547-9_8 pdf
also the kinetics correspondingly When a chemical reaction takes place in solution, the solvent is usually in so much excess that its concentration does
Business Transformation in the Chemical Industry Are you ready?
www2 deloitte com/content/dam/Deloitte/global/Documents/Energy-and-Resources/gx-chemical-business-transformation pdf
Differ- entiation and innovation trigger growth by enabling new products, solutions and applications, such as new forms of mobility, zero-energy housing,
Chemical transformations of nanostructured materials
staff ustc edu cn/~zengj/paper/31_Nano_Today_2011 pdf
Chemical transformation of existing inorganic nanostructures from one material on the chemical transformation of nanowires in solution [85—87,92—94]
Solutions for the Chemical Operations Executive - Yokogawa
web-material3 yokogawa com/1/11563/files/Solutions_for_Chemical_Operations_Executive pdf
industry and offers solutions for companies to achieve success in this evolving market Digital Transformation Availability & Uptime Aging Workforce
Filière Sciences de la Matière Chimie Cours Chimie des Solutions
www uca ma/public/files/docs/site-164-ed3ab3a20a43796f645b47e2693d7426-71270221 pdf
Solution 1 2 Concentration d'une espèce en solution : 1 2 La masse volumique 1 3 La densité 1 4 Pourcentage ou Fraction CHAPITRE II : REACTIONS
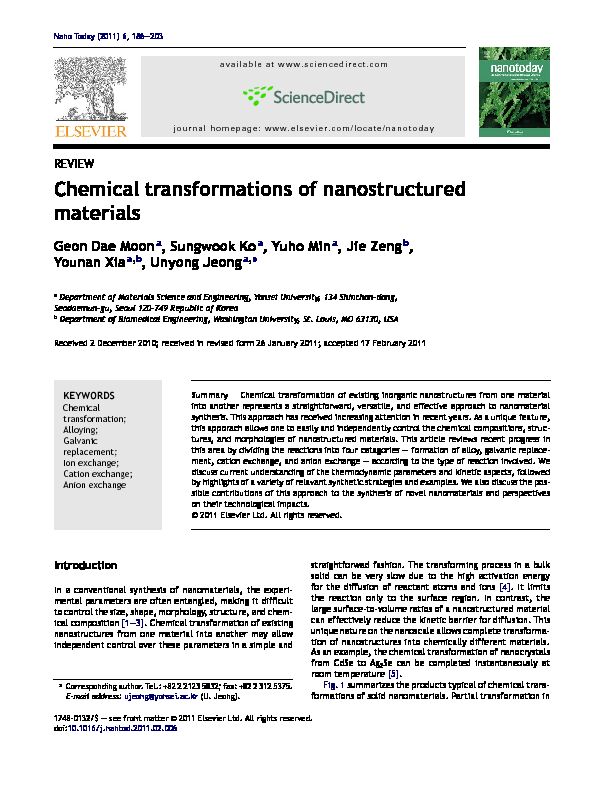
44840_631_Nano_Today_2011.pdf
Nano Today (2011)6, 186-203
available at www.sciencedirect.comjournal homepage: www.elsevier.com/locate/nanotoday
REVIEW
Chemical transformations of nanostructured
materials
Geon Dae Moon
a , Sungwook Ko a, Yuho Min a , Jie Zeng b ,
Younan Xia
a,b , Unyong Jeong a,? a Department of Materials Science and Engineering, Yonsei University, 134 Shinchon-dong,
Seodaemun-gu, Seoul 120-749 Republic of Korea
b Department of Biomedical Engineering, Washington University, St. Louis, MO 63130, USA Received 2 December 2010; received in revised form 26 January 2011; accepted 17 February 2011
KEYWORDS
Chemical
transformation;
Alloying;
Galvanic
replacement;
Ion exchange;
Cation exchange;
Anion exchangeSummaryChemical transformation of existing inorganic nanostructures from one material into another represents a straightforward, versatile, and effective approach to nanomaterial synthesis. This approach has received increasing attention in recent years. As a unique feature, this apporach allows one to easily and independently control the chemical compositions, struc- tures, and morphologies of nanostructured materials. This article reviews recent progress in this area by dividing the reactions into four catagories - formation of alloy, galvanic replace- ment, cation exchange, and anion exchange - according to the type of reaction involved. We discuss current understanding of the thermodynamic parameters and kinetic aspects, followed by highlights of a variety of relavant synthetic strategies and examples. We also discuss the pos- sible contributions of this approach to the synthesis of novel nanomaterials and perspectives on their technological impacts. © 2011 Elsevier Ltd. All rights reserved.Introduction In a conventional synthesis of nanomaterials, the experi- mental parameters are often entangled, making it difficult to control the size, shape, morphology, structure, and chem- ical composition[1-3]. Chemical transformation of existing nanostructures from one material into another may allow independent control over these parameters in a simple and ? Corresponding author. Tel.: +82 2 2123 5832; fax: +82 2 312 5375.
E-mail address:ujeong@yonsei.ac.kr(U. Jeong).
straightforwad fashion. The transforming process in a bulk solid can be very slow due to the high activation energy for the diffusion of reactant atoms and ions[4]. It limits the reaction only to the surface region. In contrast, the large surface-to-volume ratios of a nanostructured material can effectively reduce the kinetic barrier for diffusion. This unique nature on the nanoscale allows complete transforma- tion of nanostructures into chemically different materials. As an example, the chemical transformation of nanocrystals from CdSe to Ag2
Se can be completed instantaneously at
room temperature[5]. Fig. 1summarizes the products typical of chemical trans- formations of solid nanomaterials. Partial transformation in
1748-0132/$ - see front matter © 2011 Elsevier Ltd. All rights reserved.
doi:10.1016/j.nantod.2011.02.006
Chemical transformations187
Figure 1Schematic drawings showing the products of chemical transformations of solid nanomaterials. Partial trans- formation at the surface produces core-shell nanoparticles or core-sheath nanowires. Selective removal of the unreacted core and/or presence of difference in atomic diffusion rate gen- erate hollow nanostructured materials. The product may retain the initial shape of the template nanomaterials or break into small fragments. the surface region can produce core-shell nanoparticles or core-sheath nanowires. Selective removal of the unreacted cores generates hollow nanostructures. Full conversion may retain the initial shape, break the template materials into small fragments, or create hollow structures. Solid state chemical reactions for the transformation can be divided into four categories: (i) alloying (solid-solid, solid-vapor reaction), (ii) replacement reaction (solid-ion reaction), (iii) cation exchange reaction (cation-cation exchange), and (iv) anion exchange reaction (anion-anion exchange).Fig. 2illustrates the differences of the four chemical transformations. Formation of alloy is based on the diffusion of atoms formed via reduction. It can lead to solid or hollow structures depending on the diffusivity at the interface. Galvanic replacement involves simultaneous dissolution of a metal template and deposition of a sec- ond metal. It normally generates hollow structures. In ion exchange reactions, the overall morphologies are sensitive to the volume change during the transformation. So far, solid nanomaterials were mainly obtained by cation exchange reactions, and hollow nanomaterials were obtained by anion exchange reactions. Chemical transformation is a relatively new route to nanomaterial synthesis compared with the approach based onphysicaltemplating[6-11].Recentadvanceshaveproven its usefulness in generating nanostructured materials with controllable structures and chemical compositions. Impor- tantly, starting with a nanomaterial that is massively producible with environment-friendly methods, it might be possible to transform them into a wide variety of materials with different chemical compositions and structures under mildreactionconditions.Foreachoneofthechemicaltrans- formation methods, we aim to provide an overview of the current status in terms of reaction conditions and selection of materials.
Formation of alloys
The formation of a binary or multi-element alloy is thermo- dynamically determined by the phase diagram. The usual
eutectic phase diagram between two metals gives the com-positional boundary[12]. Chemical transformation in solid
thin films has long been studied by evaporating a sec- ond metal on top of pre-deposited thin films of one metal [13,14]. The uniform chemical conversion in the entire film can be achieved thanks to the reduced diffusion barrier for the reactant atoms to reach the other surface of the film. The same concept has recently been utilized for nanopar- ticles and nanowires. So far, majority of the studies has been carried out with chalcogens (O, S, Se, and Te). The driving force mainly comes from the enthalpy of forma- tion of metal chalcogenides, which is much lower than the pure components[15-17]. Transformations from both metal and chalcogen nanomaterials are useful to the preparation of various metal chalcogenides. Based on this approach, nanoparticles with various structures have been produced, including solid, hollow, yolk, and core-shell nanoparticles, as well as nanowires, nanotubes, and necklaces. The mate- rials include metal oxides (?-F 2 O 3 [18],Cu 2
O[19], CuO[20],
CoO[21], ZnO[22],Al
2 O 3 [23], and SiO 2 [24]), metal sulfides (ZnS[25], CdS[26,27], PbS[28], FePt@CoS 2 [29], and Co 3 S 4 [30]), and metal selenides or tellurides (CoSe 2 , CoTe[30], Ag 2
Se[31,32], CdSe[33],Ag
2
Te[35], CdTe[39], and PbTe
[40]). When metals are transformed into metal chalcogenides, the Kirkendall effect can play a pivotal role in determin- ing the morphology of the product. As demonstrated by Alivisatos and coworkers[21], the reaction of Co nanocrys- tals in an elemental O 2 /Ar environment resulted in the formation of hollow CoO nanoparticles. This is caused by the dominant outward diffusion of Co atoms in contrast to the slower inward diffusion of oxygen atoms. The size of the void was noticeably smaller than the initial Co nanopar- ticles, which can be explained by an inward migration of the product shell. Similar hollow oxide nanospheres were obtained from other metal nanoparticles such as Zn, Al, Cu, and Fe below a certain size[22,23,36,37]. The transfor- mation of metal nanoparticles with other chalcogens also resulted in the evolution of hollow space inside. In a very recent publication on the sulfidation of Cd, the faster out- ward diffusion of Cd led to accumulation of vacancies at the metal/sulfide interface, generating a large void in the core (Fig. 3)[26]. Gao co-workers extended this strategy to synthesize interconnected, necklace-like hollow CoSe 2 and CoTe nanoparticles by reacting Co nanoparticles with Se and Te in solution[30]. Sulfidation of Pb nanoparticles with sulfur vapor generated hollow PbS nanoparticles via the same mechanism. However, oxidation of Pb nanopar- ticles produced solid PbO particles because oxygen has a larger diffusitivity than Pb at the Pb/PbO interface[23,28]. For metal nanoparticles larger than a critical size, the oxida- tion led to the formation of metal@metal oxide core-shell solid spheres instead of generating hollow ones[36,37]. When nanostructured chalcogens are used as the start- ing materials, the Kirkendall effect is not observed because the net diffusion of atoms is inward. The high reactivity of Se and Te with various metals even at room temperature made them excellent templates for the synthesis of vari- ous metal chalcogenides. Xia and coworkers demonstrated thetransformationofmesoscalea-Sesphericalparticlesinto Se@Ag 2 Se core-shell spheres with controllable shell thick- ness[31]. In this process, Ag atoms reduced from AgNO 3 by ethylene glycol diffused into the Se particles. When the
188G.D. Moon et al.
Figure 2Illustrations showing the major differences between the concepts and principles of the four chemical transformations.
Ag 2 Se shell was thick enough, the core-shell particles pre- served the spherical shape during multiple cycles of phase transitions between-Ag 2
Se (low-temperature phase) and
˛-Ag
2 Se (high-temperature phase). This structural stability was utilized to fabricate photonic crystals with thermally switchable stop bands[31]. In addition to particles, trigonal selenium (t-Se) nanowireshavebeentransformedintoAg 2
Senanowires[32].
The transformation was conducted simply by adding AgNO 3 to at-Se nanowire suspension in ethylene glycol (Fig. 4). The topotactic lattice matching was considered to explain the fast reaction and the preservation of the single crystallinity because the Se anions did not have to experience severe rearrangement during the transformation. Partial transfor- mation at the surface area followed by selective dissolution of the Se core allowed the preparation of nanotubes such as CdSe, RuSe 2 , and Pd 17 Se 15 [33,38]. Nanowires of trigo- nal Te (t-Te) were also used as templates for the formation
of various metal tellurides[35]. Ultrathin, single-crystalTe nanowires with high aspect ratios were synthesized in
an aqueous solution. The 100% volume increase during the transformation into Ag 2
Te nanowires caused considerable
mechanical stress accumulated along the length direction and chopped the long Te nanowires (>10?m) into short ones (1?m long). The shortened Ag 2
Te nanowires preserved
the single crystallinity of the Te template nanowires. The transformation of Te nanowires into single-crystal Ag 2 Te nanowires demonstrates a good example, where homo- geneous gradual conversion can occur from the surface even in nanowires. Inhomogeneous, locally spotted initia- tion during the transformation will result in nanowires with multiple grains. As Yu and coworkers have demonstrated, ultrathin Te nanowires could also be converted into CdTe and PbTe nanowires through low-temperature hydrother- mal process[39]. In addition, relatively short Ag 2 Te, La 2 Te 3 , and Ag-doped La 2 Te 3 nanowires were synthesized by transforming Te nanowires at room temperature[41,42].
Metal telluride nanotubes such as CoTe
2 and CoTe were
Chemical transformations189
Figure 3(A) Schematic illustrating the sulfidation of Cd nanoparticles, where a solid cadmium particle was exposed to elemental
sulfur vapor. Partial sulfidation of the Cd core resulted in polycrystalline CdS shell. Further reaction led to hollow CdS structure.
(B-G) TEM images at different stages of the sulfidation. The initial Cd nanoparticles (B) to the final CdS hollow particles (G). The
scale bar is 500nm. Reproduced with permission from Ref.[26], copyright ©2008 American Chemical Society. also synthesized starting from Te nanotubes as chemical templates[43,44]. The phosphidation is another route for chemical transfor- mation from metal nanocrystals to metal phosphide. Schaak and coworkers demonstrated that Rh nanocrystals with vari- ous morphologies such as sphere, cube, octahedral, triangle, and multipods could be transformed into Rh 2
P nanocrystals
without any severe shape change[45,46]. In the same way, various metal nanocrystals have been proven to be con- verted into metal phosphides; Cu 3 P, Zn 3 P 2 , InP, GaP, Ni 2 P, Ni 5 P 4 ,Pd 5 P 2 , and PdP 2 [47]. This chemical transformation paved the way for a low-temperature alternative to synthe- sizemetalphosphidenanocrystals.Thesamegrouphavealso demonstrated that a variety of metal nanocrystals can make binary/ternary intermetallic nanocrystals including AuSn,
AuCuSn
2 , FeSn 2 , RuSn 2 , CoSn 2 , PdZn, Cu 8 Zn 5 , and Au 3 Zn [48-51].
Galvanic replacement reaction
Galvanic replacement reaction is a chemical transformation between solid metals and metal ions. It is a single-step reac- tionbasedonthedifferenceinstandardelectrodepotentials of various metals. The reaction leads to deposition of a more noble metal and dissolution of a less noble metal. For exam- ple, the standard reduction potential of AuCl 4- /Au (0.99V vs. SHE) is higher than that of Ag + /Ag (0.8V vs. SHE). Thereduction potential difference drives the replacement of Ag by Au through the following redox reaction. 3Ag (s) +AuCl - 4(aq) →Au (s) +3Ag + (aq) +4Cl - (aq) Xia and co-workers have utilized the reaction to trans- form various Ag nanostructures into Au or Au/Ag alloy nanomaterials[52,53]. The Ag nanocubes stabilized with poly(vinyl pyrrolidone) (PVP) have served as a good tem- plate for the synthesis of hollow Au nanoboxes or nanocages. When Ag nanocubes with sharp corners reacted with AuCl 4- , pinholes were created at the side faces of the Ag nanocubes (Fig. 5A)[53]. This is because the reaction is initiated at a site with the highest surface energy such as stacking faults, surface steps, point defects, or holes rather than over the entire surface. This pinhole served as an anode, at which Ag was oxidized. The released electrons were con- sumed by AuCl 4- to generate Au atoms that grow on the surface of Ag nanocubes. As the reaction proceeded, the surface holes were gradually closed through the deposition of Au atoms, which finally formed nanoboxes consisting of
Au/Ag alloy. With an excessive amount of HAuCl
4 , Ag atoms in Au/Ag nanoboxes were further dissolved to produce Au nanocages (Fig. 5B and C). When the Ag nanocubes had trun- cated corners, dissolution of Ag occurred at every corner and produced Au nanocages with uniform, well-positioned pores (Fig. 5D-F). This difference was originated from the pref-
190G.D. Moon et al.
Figure 4(A and B) TEM and HR-TEM images of thet-Se nanowires. (C and D) TEM and HR-TEM images of the Ag
2
Se nanowires
produced by chemical transformation of thet-Se nanowires. The crystal structures between these two nanowires are topotactic.
Reproduced with permission from Ref.[86], copyright ©2006 The Royal Society of Chemistry. erential binding of the stabilizing polymer (PVP) to{100} facets of the truncated Ag nanocubes[54]. For Ag nanocubes with sharp corners, the entire surface was equally passi- vated with PVP. However, for Ag nanocubes with truncated corners, the{111}corners are relatively less passivated compared to the{100}side faces. Thereby, the dissolution of Ag in the truncated nanocubes selectively took place at the corners, while the Au kept being deposited at the{100} faces. The wall thickness and pore size of the resultant Au nanocages could be controlled by adjusting the reaction time and concentration of the aqueous AuCl 4- (or AuCl 2- ) as a transforming component[55,56]. In addition to Au nanocages, Au-containing nanostruc- tures in different forms were fabricated by applying the galvanic reaction to other Ag nanostructures, including nanorings[57], triangular nanorings[58], prism-shaped nanoboxes[58-60], and single-walled nanotubes[59,60]. Multi-walled nanoshells and nanorattles were also success- fully synthesized via multistep preparation[61]. The main stepforthesynthesisofthemulti-walledstructuresincluded conformal deposition of a Ag layer on the single-walled hol- low Au nanostructure. Once a thin layer of Ag had been formed on the surface, the layer was exploited as a tem- plate for another round of galvanic replacement reaction to form the second Au shell. The Au/Ag nanoparticles were used as starting materials for the preparation of Au/Ag nanorattles by implementing more rounds of Ag coating and galvanic reaction (Fig. 6A). In the same way, multi- walled nanoshells could be prepared by repeating the Ag
shell coating and galvanic replacement (Fig. 6B). Further-more, 1D nanostructures of Ag were also used to synthesize
single- or double-walled nanotubes of Au/Ag alloys (Fig. 6C). The coaxial nanotubes with more than two walls could be obtained by following the same procedure for multi-walled nanoshells. Galvanic replacement reaction has also been successfully extended to various metal pairs with differ- ent reduction potentials. The reduction potentials of Pt 2+ /Pt (1.2V vs. SHE) and Pd 2+ /Pd (0.83V vs. SHE) are higher than that of Ag + /Ag (0.8V vs. SHE). The potential difference enabled the fabrication of Pt/Ag and Pd/Ag nanostructures. Sequential galvanic reaction generated multi-walled hybrid nanoboxes or nanotubes consisting of a Pt/Ag inner wall and a Pd/Ag alloy outer wall (Fig. 6C)[59,61-63]. As Liang and coworkers demonstrated[64], Co nanopar- ticles were also suitable templates for the synthesis of AuPtbimetallicmaterials.Theyproducedabimetallicchain- like structure through the galvanic reaction, followed by the assembly of the nanoparticles owing to the magnetic dipole interaction. Similar approach was applied to gen- erate hollow nanospheres of superparamagnetic CoPt alloy by reacting Co nanoparticles with K 2 PtCl 6 [65]. Zeng and co-workers prepared necklace-like Au, Pt, and Pd hollow nanostructures using Co nanoparticles as the chemical tem- plate[66]. Hydrophilic Co@Au yolk/shell superparamagnetic bimetallic nanospheres and their pea-like assemblies were prepared by controlled galvanic replacement reaction under externalmagneticfield[67].Veryrecently,uniformultrathin Pt nanotubes, Pt nanowires, and Pd nanowires with diam- eters of several nanometers and very high aspect ratios of ≂10,000 have been synthesized by the galvanic replacement
Chemical transformations191
Figure 5(A) Illustration showing the morphological changes of a Ag nanocube with sharp corners during a galvanic replacement
reaction with Au ions. The color change indicates the conversion of Ag into Au/Ag alloys, and then into pure Au. (B) SEM image of
pristine Ag nanocubes and their electron diffraction pattern (inset). (C) SEM image of the resultant Au nanocages. (D) Illustration
showing morphological changes involved in the formation of a Au nanocage from a Ag nanocube with rounded corners. The SEM and
TEM (inset) images of Ag nanocubes and Au nanocages with regular nanopores are shown in (E) and (F), respectively.
Reproduced with permission from Ref.[53], copyright ©2008 American Chemical Society. of ultrathin Te nanowire templates[68]. The addition of H 2 PtCl 6 , PtCl 2 (NH 3 ) 2 , and PdCl 2 into ethylene glycol suspen- sion of Te nanowires at 60 ◦
C resulted in the one dimensional
nanostructures. The reactions between Te nanowire and metal ions took place via the following mechanisms: PtCl 62-
+Te+3H 2
O→Pt+TeO
32-
+6Cl - +6H + 2PdCl 2 +Te+3H 2
O→2Pd+TeO
32-
+4Cl - +6H + The morphologies after galvanic reaction were dependent on the metal salt precursors used in the reaction and were explained by the fact that the molar ratio of Pt and Pd to Te
is determined by the valence number of the metal salt. Inaddition, the smaller molar volume of Pt (≂9cm
3 /mol) com- pared to that of Te (≂20cm 3 /mol) resulted in the tubular structure.Incontrast,onlysolidPdnanowireswereobtained since the molar volume of Pd (≂18cm 3 /2mol) was similar to that of Te at the molar ratio of 2:1 (Pd:Te).
Cation exchange reaction
The atomic bonding in multi-element inorganic materials is characterized by a mixture of covalent and ionic bond- ing. The ionic bonding is the major contribution in most compound inorganic semiconductors[69]. Such an ionic character of the elements permits exchange of the con- stituent elements by other elements in the ionic form. Most
192G.D. Moon et al.
Figure 6(A and B) Schematics and TEM images of the multi-step preparation of Au/Ag nanorattles and Au/Ag multi-walled
nanoshells, respectively (reproduced with permission from Ref.[53], copyright ©2008 American Chemical Society). (C) Schematic
of procedure (top) and SEM images of multi-walled nanotubes. Double-walled nanotubes of Au/Ag alloy (middle) and double-walled
nanotubes consisting of a Au/Ag alloy inner wall and a Pd/Ag alloy outer wall (bottom). Reproduced with permission from Ref.[62], copyright ©2004 Wiley-VCH. semiconducting materials are formed with anions serving as the structural frame and with cations that are rela- tively mobile in the crystal lattice. Therefore, exchange of cations can be achieved through simple mutual dif- fusion with other cations[4]. In comparison, the anion exchange reaction may require complete change of the crystal frame, thereby the structure can evolve into dif- ferent morphologies. Normally the high kinetic barrier for the anion exchange does not allow simple diffusion pro- cess in solution-based transformations. Therefore, most anion exchange reactions have been performed in vac- uum at high temperature or conducted in solution via indirect chemical reactions[70-73]. The concept of ion exchange reactions from pre-synthesized nanostructures can greatly expand the scope and diversify inorganic semi-
conductor nanomaterials.Table 1summarizes the chemicaltransformation of nanomaterials involving ion exchange
reactions.
Since Weller and co-workers published the use of
cation exchange to transform CdS nanoparticles into lay- ered CdS/HgS/CdS nanocrystals[74], there have been massive research publications on cation exchange reac- tions for nanocrystals, mesoscale particles, and nanowires [5,34,75-90]. In order to employ the cation exchange reac- tion as one of the efficient chemical transformations, it is important to understand the thermodynamic aspect for each transformation reaction, as well as the kinetic barrier and morphological changes. The first criterion for the thermodynamic feasibility is the solvation energy of the reactant nanomaterials, in other words, the solubility of the cations in the starting nanomate- rials. The transformation may proceed when the cations are
Chemical transformations193
Table 1Nanostructured materials obtained by ion exchange reactions.
Reaction Reactant Product Morphology
Cation exchangeAg
2
E, Se@Ag
2 Se (E=S, Se) ME, Se@MSe (M=Cd, Pb, Zn) Core"shell[78,79],NP[5],NR[5],
NW[85,86], and 2D network[87]
Ag 2
Te MTe (M=Cd, Zn, Pb) NW[35]
CdS, CdSe, CdSe/CdS M
x S, M x Se, M x Se/M x
S (M=Cu, Pb,
Ag, Zn)NP[5,95],NR[5,80,82,96],NW
[87,89],NB[92], and aerogel[87]
CdE (E=S, Se, Te) Pt
x E y ,Pd x E y
NP[88],NR[88], and NT[36]
PbE (E=S, Se) PbE@CdE Core-shell NP[95,97]
ZnS, ZnTe M
x
S, CdTe, ZnS@MS (M=Ag, Cu,
Bi, Sb, Pb, Cu)Hollow sphere[98],NP[109],NW
[110], and NT[81] Cu x
E (E=S, Se, Te) CdE, PbE, Ag
2
ENP[83,84]and NR[82]
SnSe PbSe NP[99]
Ln 1 F 3 Ln 2 F 3
NP[100]
Anion exchange
ZnO ZnO@ZnE, ZnE (E=S, Se) Hollow NP[101,108],NT[102,103] Cu x O y Cu x E y (E=S, Se) Hollow NP[106,107]
CuCl CuS NT[72]
MI 2 @SWNT (M=Cd, Zn, Pb) ME@SWNT (E=S, Se, Te) 1D inside SWNT[109]
MS (M=Cd, Pb) MS@MSe NP[104]and NW[105]
MO 3 (M=Mo, W) MS 2
Hollow NP[71]
RE(OH)
3 , RE(NO 3 ) 3 REPO 4
NP[110],NR[110], and NW[110]
M(OH) 2 (M=Cd, Ni, Fe) ME (E=O, S, Se, Te) NR[113]and NT[128,130-132] Ln, lanthanide; RE, rare-earth metal; NP, nanoparticle; NR, nanorod; NW, nanowire; NB, nanoband. fully solvated in the solution medium, albeit it cannot take place in a poor solvating medium. For example, the transfor- mation of CdE→M x E y (E=S, Se, Te; M=Pd, Pt) can proceed to a complete conversion in a polar solvent, while the reac- tion cannot take place or proceed to a very little extent in a nonpolar solvent[91]. Thereby, most cation exchange reac- tions are conducted in polar solvents. Once the reactants and products are solvated in a solution, relative solubility difference between them determines if the reactions are thermodynamically favorable or not. Ions in a solid with a relatively higher solubility can be exchanged by other ions if the product has a lower solubility. In thermodynamic terms, the solubility product (K sp ) of an ionic solid is referred to as an equilibrium constant between an ionic solid and its dissolved state. It is related to the free energy change of a solution (?G=-RTlnK sp ). Unfortunately, we do not have enough solubility product data for many pairs of ionic solids and solvents. Based on the idea that the solubilities of ionic salts show a similar trend in most polar solvents, the solu-
bility product in water can give an approximate but usefulcriterion to determine the thermodynamic possibility of a
cation exchange reaction.
Table 2summarizes theK
sp values available in litera- tures for various metal chalcogenides. From the table, it is obvious that the transformation from CdS into Ag 2
S is favor-
able, while the reverse reaction is prohibited. There is a lack ofK sp values for compounds involving Se and Te. Nor- mally, the solubility products of metal chalcogenides have a lower value as the ionic radius of chalcogen increases: K sp (M x S y )>K sp (M x Se y )>K sp (M x Te y )[35]. This order greatly limits the available cation exchange reactions.Fig. 7sum- marizes the relative order in the solubility products of various metal chalcogenides. In terms of chemical synthesis, it is fortunate that the actual solubility can be controlled by many factors[91]. The addition of a common ion of reactant and product, addition of non-common salt, tem- perature change, and ligand complexation can be used to facilitate the exchange process. Because selective increase of the solubility of a product salt can proceed with the cation exchange reaction, selective ligand complexation to Table 2Solubility products of various metal chalcogenides in descending order[35].
Solubility product constant,K
sp at 25 ◦ C
Solid E=S E=Se E=Te Solid E=S E=Se E=Te
Ag 2
E3×10
-50
1×10
-54
N.A. NiE 1×10
-21
2×10
-26 N.A. Bi 2 E 3
1×10
-100
1×10
-130
N.A. PbE 1×10
-28
1×10
-37 N.A.
CdE 1×10
-28
4×10
-35
1×10
-42
PtE 9.9×10
-74
N.A. N.A.
CuE 5×10
-36
2×10
-40
N.A. SbE 2×10
-93
N.A. N.A.
HgE 6×10
-53
4×10
-59
N.A. SnE 1×10
-26
5×10
-34 N.A. In 2 E 3
6×10
-76
N.A. N.A. ZnE 3×10
-25
1×10
-27 N.A.
194G.D. Moon et al.
Figure 7The relative order in the solubility products of various metal chalcogenides. Figure 8(A) Schematic showing the cation exchange between CdSe and Ag 2 Se. (B-D) TEM images of the initial CdSe nanocrystals, Ag 2
Se derived via a forward cation exchange reaction (C), and CdSe nanocrystals recovered using a reverse cation exchange reaction
(D). (E-G) TEM images of the initial CdTe tetrapods (E), Ag 2 Te tetrapods produced from cation exchange of CdTe (F), and CdTe recovered through a reverse cation exchange reaction (G).
Reproduced with permission from Ref.[5], copyright ©2004 American Association for the Advancement of Science.
Chemical transformations195
Figure 9(A) Schematic illustrating the synthesis of Se@Ag 2 Se core-shell colloidal spheres by reactinga-Se spheres with Ag + ,
and their transformations into Se@ZnSe, Se@CdSe, and Se@PbSe via cation exchange reactions. (B-E) SEM images of Se@Ag
2
Se (B),
Se@ZnSe (C), Se@CdSe (D), and Se@PbSe colloidal spheres (E). The insets show TEM images of the corresponding sample after the
a-Se cores had been removed with hydrazine. Reproduced with permission from Ref.[79], copyright ©2007 American Chemical Society. the product salt can be an effective approach to turn the thermodynamically unfavorable reaction into a favorable one. Alivisatos and coworkers took advantage of this con- cept and pioneered reversible cation exchange reactions between CdE and Ag 2
E (E=S, Se, Te) nanocrystals in the form
of spheres and tetrapods (Fig. 8)[4]. The reverse exchange reaction (Ag 2
E→CdE) was realized in the presence of com-
plexing molecules (TBP/TOP). Alivisatos and coworkers also investigated the structural changes of nanocrystals during the cation exchange reaction by comparing the equilibrium and non-equilibrium shapes. The reaction was immediately completed (in 1s) due to the small dimension comparable to the reaction zone (≂5nm).
Theyfoundthatthemorphologicalchangeisinevitablewhenthe size of nanocrystal is smaller than the width of reaction
zone[4]. They observed that the CdSe nanorods, CdS hollow spheres, and CdTe tetrapods over a certain size (4-5nm) maintained their initial morphologies after the exchange reactions, while thinner CdSe nanorods reconstructed into the equilibrium spherical nanocrystals. Since the structure of the anion sublattice must be changed during the cation exchange reactions, the structural difference between reac- tant and product can play a vital role in determining the activation barrier. Topotactic relation allows fast exchange of cations, while the reaction accompanying severe change in crystal structure slows down the exchange rate. Volume change during the transformation is another issue on the morphology. Son and co-workers have demonstrated that
196G.D. Moon et al.
Figure 10Transformations from ultrathin Ag
2 Te nanowires to MTe (M=Zn, Cd, Pb) through a reverse cation exchange reaction and further transformation of the CdTe nanowires into PtTe 2 nanotubes via a forward exchange reaction. (A and B) TEM and HR-TEM image of the Ag 2
Te nanowires used as the starting material. (C and D) TEM and HR-TEM images of CdTe nanowires transformed from
the Ag 2 Te nanowires. (E and F) TEM and HR-TEM images of the PtTe 2 nanotubes derived from CdTe nanowires through the forward cation exchange reaction. The inset shows the Fourier transformed ring pattern of PtTe 2 nanotubes. Reproduced with permission from Ref.[35], copyright ©2010 American Chemical Society. the final morphologies of the product nanomaterials are affected mainly by the volume change during the cation exchanges from CdE to M x E y (E=S, Se, Te; M=Pd, Pt)[77]. The product nanocrystals with large volume reduction can release the lattice stress by generating voids. Transforma- tions with large volume expansion led to fragmentation of the products into nanoparticles. The products experiencing small volume changes readily preserved the original mor- phology. After the Alivisatos group demonstrated the reversible cation exchanges for nanocrystals[4], Xia and coworkers took a similar approach to realize cation exchanges in mesoscale particles[79]. The approach successfully diver- sified the species of semiconductor mesoscale particles obtainable through a solution process. They first prepared Se@Ag 2 Se core-shell spherical particles by partially react- ing amorphous Se (a-Se) particles with Ag atoms and then transformed the shell into a variety of metal selenides to produce Se@MSe (M=Zn, Cd, Pb) core-shell particles.Fig. 9 shows a schematic (Fig. 9A) of the chemical transforma- tion froma-Se to Se@Ag 2
Se and Se@MSe. Selective removal
of the core Se generated metal selenide hollow particles. SEM and TEM images of the hollow particles are shown for Ag 2 Se, ZnSe, CdSe, and PbSe. Because the volume changes
during the transformation were small, all the productsmaintained the spherical shape with a similar diameter and
shell thickness. The partial cation exchange of ionic nanocrystals has been used to synthesize heterostructured nanocrystals, enabling investigation on the initiation and propaga- tion of exchange reaction. Heterostructured quantum dot/quantum well was demonstrated by converting CdE to
CdE/HgE (E=S, Te) through the exchange between Cd
2+ and Hg 2+ [74-76]. By controlling the cationic ratio of pre- cursor to solid salt, the partial cation exchange of CdS nanorods into CuS-Ag 2
S or CdS-Cu
2
S nanorods was success-
fully achieved. The same group observed the front line of the cation exchange reaction by monitoring the distribu- tions of Cd, Ag, and Cu atoms at the interfaces[80,81]. The resulting morphology of CdS nanorods through partial cation exchange with Ag + is a linear arrangement of regu- larly spaced Ag 2
S dots confined to the CdS rod. However,
the resultant morphology of CdS-Cu 2
S was found to be
an epitaxial attachment of Cu 2
S to the end facets of CdS
nanorods. This discrepancy in the final morphologies of CdS nanorods is due to the difference in formation energies of the CdS-Cu 2
S and CdS-Ag
2
S interfaces. While the chemi-
cal contributions for each of CdS-Cu 2
S formation energies
are positive, they are negative for each of CdS-Ag 2
S inter-
faces. In addition, the elastic contributions for all of the
Chemical transformations197
Figure 11Transformation from an array of CuCl (top) nanorods into closed-tip CuS nanotubes. (A and B) SEM and TEM images of
the CuCl nanorod array grown on a Si substrate. (C and D) An array of tubular CuS nanostructures derived from the CuCl nanorods
by reacting with H 2 S via anion exchange. The inset shows the SAED pattern of a nanorod. Reproduced with permission from Ref.[72], copyright ©2007 Elsevier B.V.
CdS-Cu
2
S interfaces are much smaller than the CdS-Ag
2 S interfaces owing to the smaller mismatch between the CdS and Cu 2 S lattices. Lastly, there is a larger energetic dif- ference between the elastic contributions of the side and end-on CdS-Ag 2
S junctions compared to the CdS-Cu
2
S junc-
tions. Sequential cation exchange can also be used to make PbS/CdS heterostructures by exploiting the fact that only Cu 2
S in CdS/Cu
2
S nanorods could be converted to PbS[82].
The cuboctahedral Cu
2-x
Se nanocrystal was investigated to
synthesize octapod-shaped CdS with arms consisting of CdE (E=S, Se, Te)[83]. Hollow CuS spheres were transformed into hollow Ag 2 SorAg 2
S/Ag heterostructures by controlling
the reduction rate of Ag + [84]. The cation exchange reactions were extended to pre- pare 1D nanostructured materials. Pristine nanowires, nanotubes, and nanobelts were employed as chemical tem-
plates for various semiconducting 1D nanomaterials withcontrollable size, composition, and crystallinity. Compared
to the easy stress relaxation in spherical particles or nanorods, nanowires with high aspect ratio possess lim- ited directions to release the lattice stress accumulated during the transformations. Especially, volume change in the longitudinal axis (length direction) accumulates severe mechanical stress during the transformation of nanowires. The structural difference between the reactants and prod- ucts can also readily generate defects which can result in kinks, shortening, and fragmentation. Therefore, the mor- phology of the product is very sensitive to the reaction kinetics that is dependent on the activation barrier mainly driven by the structural difference and volume change. This limitation initially forced the researchers to focus on the transformations accompanying small volume changes under vacuum. Single-crystalline wurtzite ZnS nanobelts were con- verted from single-crystalline wurtzite CdS nanobelts by Zn
198G.D. Moon et al.
Figure 12(A and B) TEM and HR-TEM images of the initial ZnO nanoparticles. (C and D) ZnS hollow nanoparticles obtained via an
anion exchange process. Reproduced with permission from Ref.[108], copyright ©2009 American Chemical Society. vapor transport at high temperature (800 ◦
C)[92]. While
the cation exchange from CdS to ZnS nanobelts could be completed, the reverse exchange could not be completed (only with the formation of Zn x Cd 1-x
S nanobelts) even at
1000
◦ C. The forward conversion (CdS→ZnS) was claimed thermodynamically more favorable because the enthalpy of formation was reported to be-206 and-149kJ/mol for ZnS and CdS, respectively. The same group also trans- formed CdS nanowires with various thicknesses (5-200nm in diameter) to produce composition-controlled Zn x Cd 1-x S nanowires and core-shell heterostructures, Zn-Zn x Cd 1-x S superlattices, single-crystalline ZnS nanotubes, and metal- lic Zn nanowires[87]. This size-dependent cation-exchange reaction allowed for systematic investigation of the dif- fusion mechanism. Since the report by Konenkamp and coworkers on the synthesis of M x S y (M=Cu, Ag, Bi, Sb) nan- otubes by transforming ZnS nanotubes in a solution phase [70], there have been an increasing number of reports on the chemical transformation of nanowires in solution [85-87,92-94]. Very recently, Jeong and coworkers suc- cessfully transformed ultrathin Ag 2
Te nanowires into MTe
(M=Cd, Zn, Pb) nanowires without disturbing their single
crystallinity[35,85,86](Fig. 10). Because the reaction wasthermodynamically unfavorable due to the low solubility of
Ag 2 Te nanowires compared with those of MTe (seeTable 2), the transformations were accomplished in the presence of a complexation ligand (TBP). Meanwhile, the transformation from CdTe into PtTe 2 could be readily accomplished with- out any complexation ligand since the solubility product of PtTe 2 was much smaller than that of CdTe (seeTable 2). The cation exchange reaction from Ag 2
Te nanowires into CdTe
and PbTe nanowires was completed within 1-2min, which is in contrast with the longer reaction time (≂10min) for the transition from Ag 2
Te nanowires into ZnTe nanowires
(Fig. 10C and D). The retarded reaction was attributed to the larger degree of volume change during the exchange reaction (?V/V=-0.16) which increased the kinetic bar- rier for the atomic diffusion. In the exchange reaction of
CdTe→PtTe
2 , the large volume reduction (?V/V=-0.462) resulted in the polycrystalline PtTe 2 nanotubes with≂2nm wall thickness (Fig. 10E and F). The rapid cation exchange in nanostructures allowed control of chemical composition in macroscale 2D or 3D network structures. Mallouk and co-workers have demon- strated that superstructures of nanowires fromt-Se to Ag 2 Se and CdSe could be developed from the patterneda-Se
Chemical transformations199
Figure 13(A) Schematic illustrating the transformation from a bundle of Cd(OH) 2 nanowires into a CdSe nanotube and (B) TEM image of the CdSe nanotubes. (C) Ultrathin Cd(OH) 2 nanowires grown on the surface of silica colloids and (D) chains of CdSe nanocrystals obtained by transformation from the Cd(OH) 2 nanowires via an anion exchange reaction.
Reproduced with permission from Refs.[130,132], copyright ©2009 and 2010 American Chemical Society.
islands through topotactic conversion and subsequent cation exchange[93]. Since thet-Se nanowires grow at the surface ofa-Se aggregates, the resultant Ag 2
Se and CdSe nanowires
were conformal to the surrounding topography. Another example of network nanostructure is CdSe aerogel, which was confirmed by successful conversion into Ag 2
Se gel via
cation exchange[88]. The CdSe aerogel retained the inher- ent nanoparticle properties.
Anion exchange reaction
The anion exchange reaction was first exploited to fabri- cate metal sulfides by transforming metal oxides through sulfur vapor transport. The materials could be easily dis- solved in a solution phase because the anions constitute the crystal frame in a compound semiconductor. Tenne and co-workers have demonstrated that the gas-phase reaction between MoO 3-x and H 2
S in a reducing atmo-
sphere at high temperature (800-950 ◦
C) could produce
large quantity of pure MoS 2 [71]. The fullerene-like MS 2 (M=Mo, W) derived from the MO 3-x particles suggested that the size of the resultant sulfide was determined by the size of the incipient oxide nanoparticles. Ver- tically aligned CuCl nanorods on a Si substrate were used as reactant materials for the anion exchange to make arrays of CuS nanotubes (Fig. 11)[72]. The subse- quent investigation on the chemical transformation of ZnO nanowires into ZnS nanotubes through an anion exchange made a large impact on the following research activities [102]. The chemical transformation of ZnO nanorods into
ZnO/ZnS nanocables or ZnS nanotubes was successfully per-formed via a solution-based approach[103]. CdS@CdSe
and PbS@PbSe core-shell nanocrystals were also fabri- cated using the partial exchange of S 2- and Se 2- to obtain heterostructures with compositional modulation on the nanometer scale for photovoltaic applications[104,105].
Nanoparticles or submicrometer colloids of Cu
2
O can be
a good chemical template for the formation of hol- low Cu 7 S 4 nanocages or CuS/CuSe hollow spheres through the anion exchange reaction using the Kirkendall effect [106,107]. Most recent publications on the nanostructure formation via anion exchange reaction have focused on the evolu- tion of hollow structures from the initial solid materials. As reported by Alivisatos and coworkers on single crystalline hollow ZnS nanoparticle, anion exchange of ZnO with sul- fur ions was accompanied by the nanoscale Kirkendall effect (Fig. 12)[108]. In the case where inward ion diffusion is lim- ited and the elements of core diffuse outward, a void space can be formed inside the nanoparticle. Since the diffusion of cations is normally much faster than the diffusion of anions, it is the diffusion of cations that controls the final morphol- ogy even in anion exchange reactions. Furthermore, faster diffusion of O 2- than incoming S 2- results in the formation of a hollow structure from the anion exchange reaction. Anion exchange reaction was completed in the spatially confined zone of single-walled carbon nanotubes (SWCNT)[109]. The porous channel of SWCNT enabled the anion exchange reac- tion between metal halide@SWCNT core-shell with liquid sulfur, which formed BM@SWCNT (B=Cd, Zn, Pb; M=S, Se, Te). Anionic groups consisting of multiple elements can also be exchanged with other anions. Monodisperse rare-earth orthophosphate (REPO 4 , RE=La, Eu, Tb, Y, Ho) was synthe-
200G.D. Moon et al.
sized by exchange reaction between OH - or NO 3- and PO 43-
ions via intermediate RCOO - [110].
Metal hydroxides, M(OH)
x , represent another ideal can- didates for anion exchange reactions. Metal hydroxides are obtained through controlled precipitation or hydrothermal treatment of metal nitrates[111,112]. They can be read- ily transformed into metal chalcogenides ME (E=O, S, Se, Te). Ichinose and coworkers reported an aqueous synthesis of uniform and ultrathin Cd(OH) 2 nanowires (1.9nm in diam- eter)[111]. The nanowires were synthesized by increasing the pH of a diluted Cd(NO 3 ) 2 aqueous solution with the addition of NH 3 , and then allowed evaporation of NH 3 to decrease the pH. The Cd precursor went through hydrol- ysis and condensation to form hydrated cadmium ions, or the so-called ''olation"". Cd(OH) 2 was precipitated below a critical pH in the form of ultrathin nanowires. The mor- phology of Ni(OH) 2 could be controlled as nanorods[113], nanodisks[114],microspheres[115,116],andhollowspheres [117]. Many other metal hydroxides have also been stud- ied, such as Cu(OH) 2 nanowires[118], In(OH) 3 microspheres [119], La(OH) 3 nanobelts[120], and Zn(OH) 2 nanosheets [121]. Since the synthesis is fast (typically completed within
1min) and carried out in an aqueous solution, the process
is environmentally friendly and can be readily scaled up for massive production. Furthermore, the capability of morpho- logical variation facilitates their use as excellent templates for chemical or physical transformations. These nanowires are positively charged, which can find applications such as separation of DNA fragments and composite films with neg- atively charged dye molecules, proteins, nanoparticles, or conjugated polymers[122]. Thermal oxidation of the metal hydroxides can trans- form metal hydroxides into metal oxides that are widely used as sensors[123], catalysts[124], energy conversion ele- ments[125], electrodes[126], and supercapacitors[127], among others. Geng and co-workers recently synthesized
Fe(OH)
3 nanotubes and transformed them into iron oxide magnetic nanotubes[128]. Kim and co-workers reported a template-free and seedless method for the growth of
Cd(OH)
2 nanowire bundles. They demonstrated growth of the nanowire bundles on various oxide substrates (glass, ITO, and Si wafer)[129]. The Cd(OH) 2 nanowire bundles were transformed into CdSe nanotubes by reacting with an aque- ous NaHSe solution (Fig. 13A and B). The Kirkendall effect due to the relatively faster diffusion of Cd 2+ ions than that of Se 2- ions fostered the generation of voids[130,131]. Very recently, Jeong and coworkers succeeded in producing ultra- thin and long Cd(OH) 2 nanowires (≂4nm in diameter) on suspended silica colloids in basic aqueous solution (Fig. 13C) [132]. The chemical transformation of the ultrathin Cd(OH) 2 nanowires into CdSe took place with a series of locally spotted transformations along the nanowires rather than a homogeneous transformation. The volume reduction dur- ing the transformation led to chain-like CdSe nanocrystals connected with a thin CdSe string (Fig. 13D).
Conclusion and outlooks
Solid inorganic nanomaterials reduced diffusion barriers so that other atoms and ions can rapidly diffuse into and out
of the nanomaterials. For example, atoms from a reductionreaction can diffuse into solid metals or semiconductors to
form a variety of compound semiconductors. Solid or hol- low structures can be obtained depending on the relative diffusivity at the interface front. Metal ions with higher reduction potential can accept electrons from a solid metal with lower reduction potential, that is, more noble metal ions can be reduced into a solid by taking electrons from a less noble metal solid. This well-known electrochemical process opened the door to preparation of novel metallic nanomaterials such as nanocages, multi-walled nanotubes, and bimetallic nanoparticles and porous nanowires. Cations dissolved in a solvent may replace cations in a compound semiconductor if the solubility of the reactant semiconduc- tor is adjusted to be higher than the product. Basically such transformation is widely applicable between various atomic species because the solubilities of solid materi- als are selectively tunable with the proper selection of a complexation agent. The overall morphology of the cation exchange reaction is determined by the volume change dur- ing the transformation. Similar exchange can take place between anionic groups. Since the anionic groups serve as the framework of most semiconductors, most anion exchange reactions have been conducted in vacuum at high temperatures. Recent successes of the anion exchange reac- tion in solution phases greatly enlarged the scope of ion exchange reactions. During the past 20 years, synthesis of nanostructured materials has been focused on the control of size, shape, structure, and chemical composition. We have accumu- lated considerable understanding of the thermodynamic parameters and kinetic aspects. Such knowledge, how- ever, does not necessarily mean that we can independently control all these parameters of the nanostructured mate- rials. Chemical transformation is a promising approach for engineering the composition and other parameters at a fixed shape and size. In a recent publication, Bawendi and co-workers have demonstrated that chemical transforma- tion is a promising route for tuning the composition and properties of nanostructured materials by controlling the conductivity of a Ag 2
Se nanowire network during the trans-
formation from CdSe into Ag 2
Se[94]. Partial transformation
or targeted local transformation can readily produce het- erostructured nanoparticles and nanowires, which provides versatile modulation of the chemical or physical properties [133]. Very recently, the transformations between chalco- genide nanowires via alloy formation and cation exchange reactions were reported to preserve the single crystallinity of the initial nanowires[35,86,87]. These experimental results showed the possibility that chemical transformation can be used for fabricating electronic devices. Combining chemical transformation with aligned nanowires or pattern- ing of inorganic materials may facilitate the fabrication of electronic devices with tunable optical or electrical properties. In spite of the successful advances in the syn- thesis of nanoparticles and nanowires, the main obstacles to realizing practical uses are found in the difficulty of massive production and environment-friendly synthetic pro- cess. Normally, fine controls of structure and compositions have been achieved in small quantity of organic solvents at high temperatures. The templating materials for the chemical transformations are often readily obtainable in massive amount in aqueous conditions at low temperatures.
Chemical transformations201
Such templates can include nanoparticles, nanoplates, and nanowires made of chalcogens, metal hydroxides, and met- als. The products may be used as pastes to fabricate thin lms of metal chalcogenide semiconductors or metal oxides. Since the template products are soluble due to the surface charges created during the synthesis, it is useful to pro- duce composite materials with organic molecules, polymers, ceramics, or other charged nanostructured materials. The study of chemical transformations at the nanoscale is stillinanearlystageofdevelopment.Thestructuralchanges accompanying chemical transformations and the accessible crystal structures still need to be identied and understood. The diffusion kinetics involved in a chemical transformation needs to be thoroughly investigated before one can obtain controlled heterostructures. Publications on the chemical transformations of nanomaterials are rapidly increasing in recent years. The diversity of nanomaterials that can be implemented for chemical transformations are expected to expand and this approach has the potential to emerge as one of the major synthetic methods for functional nanoma- terials.
Acknowledgements
This work was supported in part by a National Research Foundation (NRF) grant funded through the World Class Uni- versity(WCU)Program(R32-20031),agrantfromthePioneer Research Program (008-05103), and a grant from the Funda- mental R&D Program for Core Technology of Materials. All these programs are sponsored by the Korean Government (MEST, MKE).
References
[1] B.L. Cushing, V.L. Kolesnichenko, C.J. O"Connor, Chem. Rev.
104 (2004) 3893.
[2] C.B. Murray, C.R. Kagan, M.G. Bawendi, Annu. Rev. Mater. Sci.
30 (2000) 545.
[3] A.L. Rogach, Semiconductor Nanocrystal Quantum Dots: Syn- thesis, Assembly, Spectroscopy and Applications, Springer
Wien, New York, 2008.
[4] S. Feng, R. Xu, Acc. Chem. Res. 34 (2001) 239. [5] D.H. Son, S.M. Hughes, Y. Yin, A.P. Alivisatos, Science 306 (2004) 1009. [6] M. Steinhart, Z.H. Jia, A.K. Schaper, R.B. Wehrspohn, U.
Gosele, J.H. Wendorff, Adv. Mater. 15 (2003) 706.
[7] C.R. Martin, Science 266 (1994) 1961. [8] R.R. He, M. Law, R. Fan, F. Kim, P. Yang, Nano Lett. 2 (2002) 1109.
[9] Y. Yin, Y. Lu, Y. Sun, Y. Xia, Nano Lett. 2 (2002) 427. [10] B. Mayers, X. Jiang, D. Sunderland, B. Cattle, Y. Xia, J. Am.
Chem. Soc. 125 (2003) 13364.
[11] C.K. Erdonmez, Y. Yin, Functional Nanomaterials: A Chemistry and Engineering Perspective, The Press of the University of
Science and Technology of China, 2009.
[12] M. Tisza, Physical Metallurgy for Engineers, ASM International and Freund Publishing House, 2002. [13] G. Ottaviani, J. Vac. Sci. Technol. 16 (1979) 1112. [14] N. Martensson, R. Nyholm, H. Calen, J. Hedman, B. Johans- son, Phys. Rev. B 24 (1981) 1725. [15] T. Takahashi, O. Yamamoto, J. Electrochem. Soc. 117 (1970) 1. [16] I. Karakaya, W.T. Thompson, J. Phase Equilibr. 12 (1991) 56.
[17] S. Deore, F. Xu, A. Navrotsky, Am. Mineral. 93 (2008) 779.[18] T. Hyeon, S.S. Lee, J. Park, Y. Chung, H.B. Na, J. Am. Chem.
Soc. 123 (2001) 12798.
[19] M. Yin, C.-K. Wu, Y. Lou, C. Burda, J.T. Koberstein, Y. Zhu, S.
O"Brien, J. Am. Chem. Soc. 127 (2005) 9506.
[20] Y. Chang, M.L. Lye, H.C. Zeng, Langmuir 21 (2005) 3746. [21] Y. Yin, R.M. Rioux, C.K. Erdonmez, S. Hughes, G.A. Somorjai,
A.P. Alivisatos, Science 304 (2004) 711.
[22] R. Nakamura, J.-G. Lee, D. Tokozakura, H. Mori, H. Nakajima,
Mater. Lett. 61 (2007) 1060.
[23] R. Nakamura, D. Tokozakura, H. Nakajima, J.-G. Lee, H. Mori,
J. Appl. Phys. 101 (2007) 074303.
[24] A. Colder, F. Huisken, E. Trave, G. Ledoux, O. Guillois, C. Reynaud, H. Hofmeister, E. Pippel, Nanotechnology 15 (2004) L1. [25] H.F. Shao, X.F. Qian, Z.K. Zhu, J. Solid State Chem. 178 (2005) 3522.
[26] A. Cabot, R.K. Smith, Y. Yin, H. Zheng, B.M. Reinhard, H. Liu,
A.P. Alivisatos, ACS Nano 2 (2008) 1452.
[27] Q. Li, R.M. Penner, Nano Lett. 5 (2005) 1720. [28] Y. Wang, L. Cai, Y. Xia, Adv. Mater. 17 (2005) 473. [29] J.H. Gao, G.L. Liang, B. Zhang, Y. Kuang, X.X. Zhang, B. Xu,
J. Am. Chem. Soc. 129 (2007) 1428.
[30] J.H. Gao, B. Zhang, X.X. Zhang, B. Xu, Angew. Chem. Int. Ed.
45 (2006) 1220.
[31] U. Jeong, Y. Xia, Angew. Chem. Int. Ed. 44 (2005) 3099. [32] B. Gates, Y. Wu, Y. Yin, P. Yang, Y. Xia, J. Am. Chem. Soc. 123 (2001) 11500. [33] X. Jiang, B. Mayers, T. Herricks, Y. Xia, Adv. Mater. 15 (2003) 1740.
[34] H. Tan, S.P. Li, W.Y. Fan, J. Phys. Chem. B 110 (2006) 15812. [35] G.D. Moon, S. Ko, Y. Xia, U. Jeong, ACS Nano 4 (2010) 2307. [36] C.M. Wang, D.R. Baer, L.E. Amonette, S. Thevuthasan, J. Anthony, Y. Qiang, Microsc. Microanal. 11 (2005) 1994. [37] C.M. Wang, D.R. Baer, L.E. Thomas, J.E. Amonette, J. Antony, Y. Qiang, G. Duscher, J. Appl. Phys. 98 (2005) 094308. [38] X. Jiang, B. Mayers, Y. Wang, B. Cattle, Y. Xia, Chem. Phys.
Lett. 385 (2004) 472.
[39] H.-W. Liang, S. Liu, Q.-S. Wu, S.-H. Yu, Inorg. Chem. 48 (2009) 4927.
[40] G. Tai, B. Zhou, W. Guo, J. Phys. Chem. C 112 (2008) 11314. [41] A.K. Samal, T. Pradeep, J. Phys. Chem. C 113 (2009) 13539. [42] A.K. Samal, T. Pradeep, J. Phys. Chem. C 114 (2010) 5871. [43] J. Li, X. Tang, L. Song, Y. Zhu, Y. Qian, J. Cryst. Growth 311 (2009) 4467. [44] H. Fan, Y.G. Zhang, M.F. Zhang, X.Y. Wang, Y. Qian, Cryst.
Growth Des. 8 (2008) 2838.
[45] A.E. Henkes, Y. Vasquez, R.E. Schaak, J. Am. Chem. Soc. 129 (2007) 1896. [46] A.E. Henkes, R.E. Schaak, Inorg. Chem. 47 (2008) 671. [47] A.E. Henkes, R.E. Schaak, Chem. Mater. 19 (2007) 4234.
[48] B.M. Leonard, R.E. Schaak, J. Am. Chem. Soc. 128 (2006)
11475.
[49] N.H. Chou, R.E. Schaak, J. Am. Chem. Soc. 129 (2007) 7339. [50] N.H. Chou, R.E. Schaak, Chem. Mater. 20 (2008) 2081. [51] R.E. Cable, R.E. Schaak, Chem. Mater. 19 (2007) 4098. [52] X. Lu, J. Chen, S.E. Skrabalak, Y. Xia, Proc. ImechE 221 (2008) 1. [53] S.E. Skrabalak, J. Chen, Y. Sun, X. Lu, L. Au, C.M. Cobley, Y.
Xia, Acc. Chem. Res. 41 (2008) 1587.
[54] J. Chen, J.M. McLellan, A. Siekkinen, Y. Xiong, Z.-Y. Li, Y. Xia,
J. Am. Chem. Soc. 128 (2006) 14776.
[55] L. Au, X. Lu, Y. Xia, Adv. Mater. 20 (2008) 2517. [56] Y. Sun, B. Mayers, T. Herricks, Y. Xia, Nano Lett. 3 (2003) 955. [57] X. Lu, H.-Y. Tuan, J. Chen, Z.-Y. Li, B.A. Korgel, Y. Xia, J. Am.
Chem. Soc. 129 (2007) 1733.
[58] Y. Sun, Y. Xia, Adv. Mater. 15 (2003) 695. [59] Y. Sun, B. Mayers, Y. Xia, Nano Lett. 2 (2002) 481.
202G.D. Moon et al.
[60] Y. Sun, B. Mayers, Y. Xia, Adv. Mater. 15 (2003) 641. [61] Y. Sun, B. Wiley, Z.-Y. Li, Y. Xia, J. Am. Chem. Soc. 126 (2004) 9399.
[62] Y. Sun, Y. Xia, Adv. Mater. 16 (2004) 264. [63] J. Chen, B. Wiley, J. McLellan, Y. Xiong, Z.-Y. Li, Y. Xia, Nano
Lett. 5 (2005) 2058.
[64] H.P. Liang, Y.G. guo, H.M. Zhang, J.S. Hu, L.J. Wan, C.L. Bai,
Chem. Commun. (2004) 1496.
[65] Y. Vasquez, A.K. Sra, R.E. Schaak, J. Am. Chem. Soc. 127 (2005) 12504. [66] J. Zeng, J. Huang, W. Lu, X. Wang, B. Wang, S. Zhang, J. Hou,
Adv. Mater. 19 (2007) 2172.
[67] Y. Lu, Y. Zhao, L. Yu, L. Dong, C. Shi, M.J. Hu, Y.J. Xu, L.P.
Wen, S.H. Yu, Adv. Mater. 22 (2010) 1407.
[68] H.W. Liang, S. Liu, J.Y. Gong, S.B. Wang, L. Wang, S.H. Yu,
Adv. Mater. 21 (2009) 1850.
[69] B.G. Yacobi, Semiconductor Materials: An Introduction to Basic Principles, Kluwer Academic/Plenum Publishers, New
York, 2003.
[70] L. Dloczik, R. Konenkamp, Nano Lett. 3 (2003) 651. [71] Y. Feldman, G.L. Frey, M. Homyonfer, V. Lyakhovitskaya, L. Margulis, H. Cohen, G. Hodes, J.L. Hutchison, R. Tenne, J.
Am. Chem. Soc. 118 (1996) 5362.
[72] Q. Wang, J.-X. Li, G.-D. Li, X.-J. Cao, K.-J. Wang, J.-S. Chen,
J. Cryst. Growth 299 (2007) 386.
[73] M. Ye, H. Zhong, W. Zheng, R. Li, Y. Li, Langmuir 23 (2007) 9064.
[74] A. Mews, A. Eychmueller, M. Giersig, D. Schooss, H. Weller, J.
Phys. Chem. 98 (1994) 934.
[75] M.T. Harrison, S.V. Kershaw, M.G. Burt, A. Eychmuller, H. Weller, A.L. Rogach, Mater. Sci. Eng. B 69"70 (2000) 355.
[76] S.V. Kershaw, M. Burt, M. Harrison, A. Rogach, H. Weller, A.
Eychmuller, Appl. Phys. Lett. 75 (1999) 1694.
[77] S.E. Wark, C.-H. Hsia, D.H. Son, J. Am. Chem. Soc. 130 (2008) 9550.
[78] U. Jeong, J.U. Kim, Y. Xia, Nano Lett. 5 (2005) 937. [79] P.H.C. Camargo, Y.H. Lee, U. Jeong, Z. Zou, Y. Xia, Langmuir
23 (2007) 2985.
[80] R.D. Robinson, B. Sadtler, D.O. Demchenko, C.K. Erdonmez, L.-W. Wang, A.P. Alivisatos, Science 317 (2007) 355. [81] B. Sadtler, D.O. Demchenko, H. Zheng, S.M. Hughes, M.G. Merkle, U. Dahmen, L.-W. Wang, A.P. Alivisatos, J. Am. Chem.
Soc. 131 (2009) 5285.
[82] J.M.Luther,H.Zheng,B.Sadtler,A.P.Alivisatos,J.Am.Chem.
Soc. 131 (2009) 16851.
[83] S. Deka, K. Miszta, D. Dorfs, A. Genovese, G. Bertoni, L.
Manna, Nano Lett. 10 (2010) 3770.
[84] M. Pang, J. Hu, H.C. Zeng, J. Am. Chem. Soc. 132 (2010)
10771.
[85] U. Jeong, Y. Xia, Y. Yin, Chem. Phys. Lett. 416 (2005) 246. [86] U. Jeong, P.H.C. Camargo, Y.H. Lee, Y. Xia, J. Mater. Chem.
16 (2006) 3893.
[87] B. Zhang, Y. Jung, H.-S. Chung, L.V. Vugt, R. Agarwal, Nano
Lett. 10 (2010) 149.
[88] Q. Yao, I.U. Arachchige, S.L. Brock, J. Am. Chem. Soc. 131 (2009) 2800. [89] S.Y. Jang, et al., ACS Nano 4 (2010) 2391. [90] W.I. Park, H.S. Kim, S.Y. Jang, J. Park, S.Y. Bae, M. Jung, H.
Lee, J. Kim, J. Mater. Chem. 18 (2008) 875.
[91] S. Lewin, The Solubility Product Principle: An Introduction to Its Uses and Limitations, Sir Isaac Pitman & Sons, London, 1960.
[92] J.Y. Lee, D.S. Kim, J. Park, Chem. Mater. 19 (2007) 4663.
[93] R. Ma, Y. Wang, T.E. Mallouk, Small 5 (2009) 356. [94] A. Dorn, P.M. Allen, D.K. Harris, M.G. Bawendi, Nano Lett. 10 (2010) 3948.[95] J.M. Pietryga, D.J. Werder, D.J. Williams, J.L. Casson, R.D. Schaller, V.I. Klimov, J.A. Hollingsworth, J. Am. Chem. Soc.
130 (2008) 4879.
[96] P.K. Jain, L. Amirav, S. Aloni, A.P. Alivisatos, J. Am. Chem.
Soc. 132 (2010) 9997.
[97] M. Ethayaraja, R. Bandyopadhyaya, Ind. Eng. Chem. Res. 47 (2008) 5982. [98] Y. Shi, J. Chen, P. Shen, J. Alloys Compd. 441 (2007) 337. [99] M.V. Kovalenko, et al., Angew. Chem. Int. Ed. 47 (2008) 3029.
[100] C. Dong, F.C.J.M. van Veggel, ACS Nano 3 (2009) 123. [101] F. Dawood, R.E. Schaak, J. Am. Chem. Soc. 131 (2009) 424. [102] L. Dloczik, R. Engelhart, K. Ernst, S. Fiechter, I. Sieber, R.
Konenkamp, Appl. Phys. Lett. 78 (2001) 3687.
[103] C. Yan, D. Xue, J. Phys. Chem. B 110 (2006) 25850. [104] Y. Xie, P. Yan, J. Lu, Y. Qian, S. Zhang, Chem. Commun. (1999) 1969.
[105] D.S. Koktysh, J.R. McBride, S.K. Dixit, L.C. Feldman, S.J.
Rosenthal, Nanotechnology 18 (2007) 495607.
[106] H. Cao, X. Qian, C. Wang, X. Ma, J. Yin, Z. Zhu, J. Am. Chem.
Soc. 127 (2005) 16024.
[107] M. Pang, H.C. Zeng, Langmuir 26 (2010) 5963. [108] J. Park, H. Zheng, Y.-W. Jun, A.P. Alivisatos, J. Am. Chem.
Soc. 131 (2009) 13943.
[109] A.A. Eliseev, et al., Chem. Mater. 21 (2009) 5001. [110] H.-X. Mai, Y.-W. Zhang, L.-D. Sun, C.-H. Yan, Chem. Mater. 19 (2007) 4514. [111] I. Ichinose, K. Kurashima, T. Kunitake, J. Am. Chem. Soc. 126 (2004) 7162. [112] B. Tang, L. Zhuo, J. Ge, J. Niu, Z. Shi, Inorg. Chem. 44 (2005) 2568.
[113] K. Matsui, T. Kyotani, A. Tomita, Adv. Mater. 14 (2002) 1216.
[114] Y. Li, B. Tan, Y. Wu, Chem. Mater. 20 (2008) 567. [115] M.T. Buscaglia, V. Buscaglia, C. Bottino, M. Viviani, R. Fournier, M. Sennour, S. Presto, R. Marazza, P. Nanni, Cryst.
Growth Des. 8 (2008) 3847.
[116] D.-B. Kuang, B.-X. Lei, Y.-P. Pan, X.-Y. Yu, C.-Y. Su, J. Phys.
Chem. C 113 (2009) 5508.
[117] S. Zhang, H.C. Zeng, Chem. Mater. 21 (2009) 871. [118] Y. Ni, H. Li, L. Jin, J. Hong, Cryst. Growth Des. 9 (2009) 3868. [119] B. Li, Y. Xie, M. Jing, G. Rong, Y. Tang, G. Zhang, Langmuir 22 (2006) 9380. [120] C. Hu, H. Liu, W. Dong, Y. Zhang, G. Bao, C. Lao, Z.L. Wang,
Adv. Mater. 19 (2007) 470.
[121] X. Hu, Y. Masuda, T. Ohji, K. Kato, J. Am. Ceram. Soc. 93 (2010) 881. [122] I. Ichinose, J. Huang, Y.-H. Luo, Nano Lett. 5 (2005) 97. [123] Q. Wan, Q.H. Li, Y.J. Chen, T.H. Wang, X.L. He, J.P. Li, C.L.
Lin, Appl. Phys. Lett. 84 (2004) 3654.
[124] J.B. Reitz, E.I. Solomon, J. Am. Chem. Soc. 120 (1998) 11467. [125] M. Law, L.E. Greene, J.C. Johnson, R. Saykally, P.D. Yang, Nat.
Mater. 4 (2005) 455.
[126] P. Poizot, S. Laruelle, S. Grugeon, L. Dupont, J.-M. Tarascon,
Nature 407 (2000) 496.
[127] K.-W. Nam, W.-S. Yoon, K.-B. Kim, Electrochim. Acta 47 (2002) 3201.
[128] Q. Wang, B. Geng, S. Wang, Y. Ye, B. Tao, Chem. Commun. 46 (2010) 1899. [129] V.R. Shinde, H.-S. Shim, T.P. Gujar, H.J. Kim, W.B. Kim, Adv.
Mater. 20 (2008) 1008.
[130] H.-S. Shim, V.R. Shinde, J.W. Kim, T.P. Gujar, O.-S. Joo, H.J.
Kim, W.B. Kim, Chem. Mater. 21 (2009) 1875.
[131] V.R. Shinde, T.P. Gujar, T. Noda, D. Fujita, C.D. Lokhande,
O.-S. Joo, J. Phys. Chem. C 113 (2009) 14179.
[132] S. Ko, J.W. Kim, G.D. Moon, H.-S. Shim, W.B. Kim, U. Jeong,
Langmuir 26 (2010) 4377.
[133] L. Carbone, P.D. Cozzoli, Nano Today 5 (2010) 449.
Chemical transformations203
Geon Dae Moonreceived a B.S. degree in
the Dept. of Materials Science and Engi- neering from Yonsei University in 2006. He received his Ph.D. in the same department under the supervision of Prof. Unyong Jeong in 2011. During his Ph.D. in 2010, he had worked as a researcher in Washington Univer- sity in Prof. Younan Xia group to investigate the synthesis of noble nanostructures for bio- applications. His research interests include synthesis of chalcogens, metal chalcogenide nanomaterials, and self-assembly of inorganic nanostructures.
Sungwook Koreceived a B.S. degree in the
Dept. of Materials Science and Engineering
in Yonsei University, Korea. He is currently pursuing his Ph.D. degree in the same depart- ment under the supervision of Prof. Unyong
Jeong. His current research is focused on the
morphology control of semiconductor materi- als for the application of thin film transistors (TFTs) and gas sensors.
Yuho Minwas born in Seoul, Korea in 1984.
He received his B.S. degree in materials sci-
ence and engineering from Yonsei University in 2010. He is currently pursuing his Ph.D. degree under the supervision of Prof. Unyong
Jeong in the same department. His research
interests focus on the synthesis of nanos- tructured materials and design